906-138
September 2, 2002
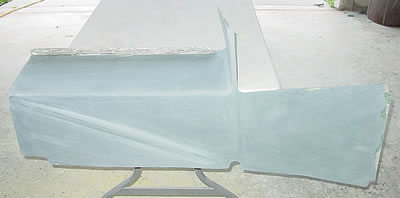
After
a few days at work, gray duratech was painted over the cockpit
surface.
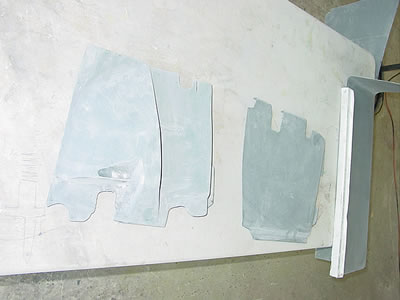
These
are the two front panels, the one on the left surrounds the
dead pedal and the one on the right would be positioned about
the passengers feet.
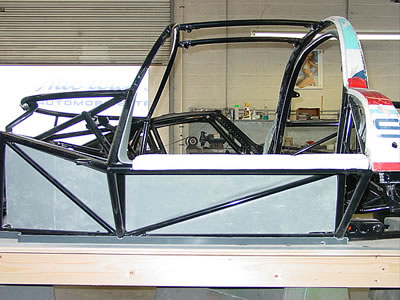
The inside
of the panels were reskined with a German S-weave. We used
gray pigment which matches the gray paint that will be brushed
on not sprayed.
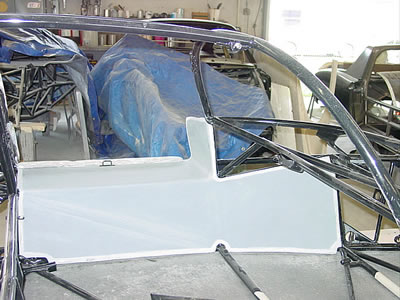
If you
look closely you can see the edges were sanded with 36 grit
sand paper for better adhesion when the door seal is glued
to all of the surrounding areas. We will use approximately
60mm wide 1-1/2 oz fiberglass mat to make all of the panel
connections.
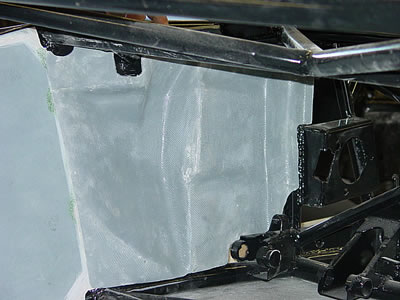
The dead
pedal panel, which you could see in one of the above pictures,
is actually made in reverse to the other cockpit panels. This
means all of the panels inside the car, with the exception
of the two front kick panels and the floor, are smooth on
the inside. If you notice in the picture, the back smooth
piece is the door seal and the front panel which will be glued
with a mat patch has the cloth surface on the side you are
looking at.
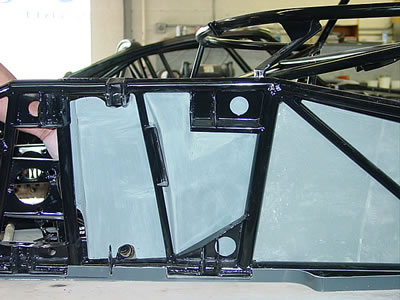
Note, the same
panel is now smooth and the door seal panel to the right has
the cloth surface.
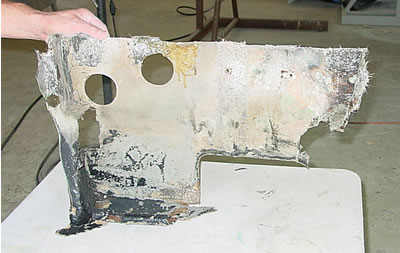
Some pieces are
easier remade than repaired.
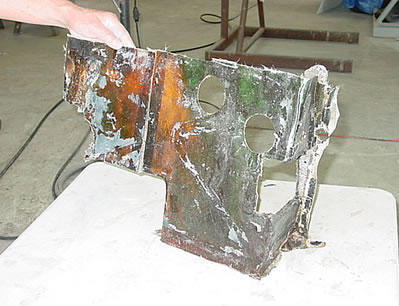
We
have molds for most of the Porsche prototypes and now and
again we get to use them.
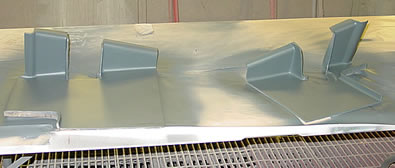
Luckily, these
two front kick panel molds (which are seen just painted with
gray duratech) are owned by a friend, John Corson, who is
quite a good race mechanic and Porsche restorer. Thanks again
John.
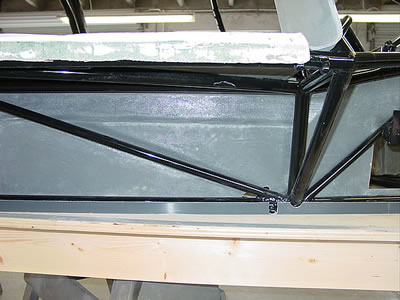
We
wouldn't have to paint the Porsche factory gray (rustoleum
navy gray) because of the gray pigmented panels, but Porsche
painted the cockpit and glass panels gray before customers
received them.
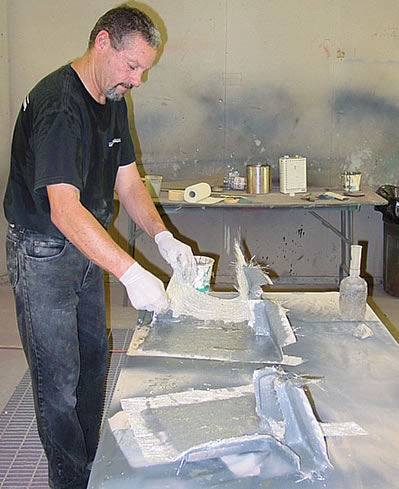
Notice,
I am not wearing respirator because this is a down draft spray
booth, thus making the nasty fumes go through the grates in
the floor long before I breath them. Also, it is about 9,000
degrees inside here Labor Day morning at about 9:15 Florida
time, and if I were to put a mask on sweat would pour off
of my face onto these parts. I guess someone in a hundred
years might be able to prove Kevin built this part through
his sweat DNA.
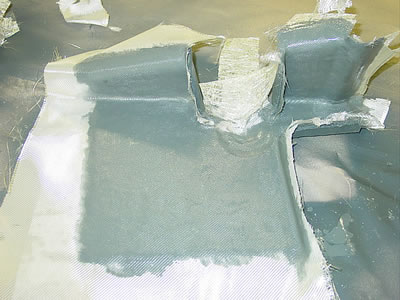
The part is now
finished and will be trimmed before it is removed from the
mold.
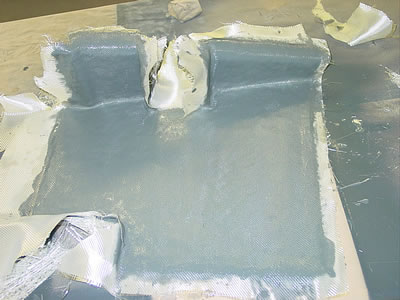
The
curing or drying of the part can be adjusted by the amount
of hardener (M.E.K). In this case, I wanted the parts to install
later in the afternoon, so I kicked it pretty fast. On parts
that have no great structural need speeding up the cure does
not effect the brittleness of the glass. If this were something
like a fender or a wing the cure would take approximately
6 hours to touch and 10 hours minimum before removing from
the mold. This is the process that we use in the summer in
Florida other climates would be different.
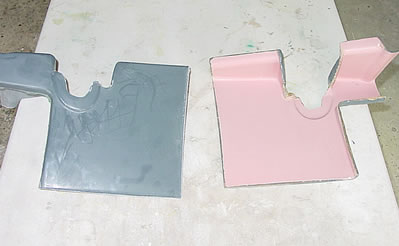
The part was removed
at 4:00 and I will install it after Kristie, Sharon (she is
about to become the new reluctant webmaster because Kristie
is going back to school), and myself the web "talker"
are finished with this update.
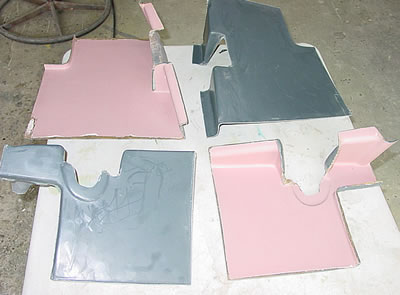
Here are the two
pieces and the molds side by side. Just for reference it took
me about 5 hours to make the parts and install them, if I
had to save the old parts it would take about 10-15 hours.
<<
Previous Update | Next Update >>