906-127
July 9, 2004
I've been
making fiberglass parts all week.
Here, I'm making the front inner fender and waxing the cooler
cover mold.
The picture
on the left is the trimmed part still in the mold. The other,
is the part removed from the mold. Earlier I made the inner
structure, which I will laminate to the hood while it sits
on the car.
The easiest
way to remove a part from the mold is a blast of air.
The part
normally just pulls right off. Here is the stack of parts
which include: door skins, inner fenders, and the front hood.
The placement
of the main body always takes two or three men to carry it
and place it on the chassis. That's the easy part. It will
take me days to fit the nose and more to attach it because
of all the necessary parts and panels that get glued together.
So far,
so good.
The boys
are peeling the PVA mold release from the duratech surface.
This product is water soluble, but it's easier just to pull
it off like sunburned skin.
Today
I've begun fitting the door sills and the inner front wheel
wells. By the end of the weekend, I should be gluing the cockpit
panels to the chassis. Next week we'll concentrate on attaching
the body to the chassis.
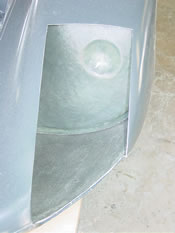
The headlight buckets get glued in before the fender panels.
It's impossible to do this process in reverse. Next week I
will start repairing the firewall, which is the one mold I've
never had. I will use my original firewall as a plug to make
the mold and then I'll make the part. This part needs to be
attached before the body gets glued on. Lots of steps to finish
the glasswork, but lots of fun doing it.
<<<
Previous Update | Next Update
>>>